|
 |
|
|
|
CEMENT
PLANTS
Portland Cement Clinker Grinding Plants
|
When the large initial capital investment is a hindrance
or the local limestone availability for manufacturing of
cement is an issue, Portland Cement Clinker Grinding
Plants is the only answer. The Raw
clinker available with ease in large quantities is grinded
to produce Portland cement. A Clinker grinding plant is a
straight forward process.
The clinker is transported to feed hopper, which feeds it
into the Pre-crusher, Table feeders extract it out form
the pre-crusher and feed it into a Ball
mill, Blending of this fine powder with gypsum and other
additives makes it the portland cement, Packing Plant and Material Handling equipment
completes the offers.
SABKO INDUSTRIES GROUP offers clinker grinding plants from 50 TPD to
3000 TPD on turn key basis.
|
|
Salient
Features
|
Low Installed Cost.
Power efficient.
Optimum
Performance.
|
|
Near Zero
Maintenance.
Lower
cost of Production.
Strong & Robust
construction.
|
|
|
|
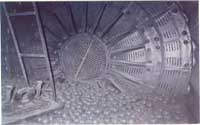 |
|
Mill
Shell:
Heavy duty steel plates are rolled to form the
Mill Shells; the rollers and pressing machines
are used to maintain the shape of the
shell perfectly during the manufacturing.
Precise templates ensure the holes for liners are drilled
in perfect distribution.
X-ray
quality welding
eliminates any chances of cracks or creceps.
|
|
|
|
Liners
:
The High
Carbon Steel, Cast Manganese Steel and Ni-hard
liners are essential part of the mills and
are designed to give optimum production.
Diaphragm
:
Ensuring the optimum level of
material filling ratio in each chamber of Ball
Mills is the key to high performance and
maximum use of grinding energy of the Mill.
|
|
|
|
|
|
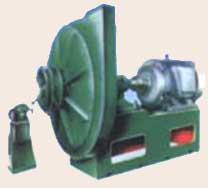 |
|
Drive
Unit:
Consists of fine cast steel finish
EN Grade trusted steel shaft housed in spherical
roller bearings is coupled with Hob-cut girth
gear and EN-19 pinion.
Larger mills of 125 HP and up require to be
driven with
helical or worm reduction gearboxes coupled with motor as shown
in the figure.
|
|
|
|
|
|
|
|
|
Suitable
Raw Materials
|
1. |
Clinker
(Minimum) |
: |
CaO
60% |
2. |
Gypsum
(Minimum) |
: |
CaSO2.2H2O 75% |
|
|
Manufacturing Process |
1) Crushing & Storage:
The pay loader carried raw materials, Clinker
and Gypsum are carried from stock yards and
dumps into a dump
hopper. A Vibro-feeder
controls feed rate. The Granulator which is
feed by means of a belt conveyor Crushes, and
then stores into the respective Silos/Hoppers
by means of a Bucket elevator. The table
feeder than feeds the
crushed material in the
desired proportion to the Ball Mill hopper.
2. Cement
Milling:
The mix is intermediately stored to the Ball
mill hopper by a Bucket Elevator. A mill
feeder is installed to control the
feed rate
to mill, and adjust the desired fineness. The
ball mill grinds the mixture which can now be
called
Portland cement. The Cement thus
produced is stored into the Cement Silos. To
ensure homogenized and consistent quality of
cement, the same is blended through the
aeration assemblies.
3) Packing:
The Screw Feeders extract and transport the
Cement to the Packing Plant where a
preliminary screening removes any
foreign/unwanted particle and than stores it
into a hopper where it is packed with the help
of Auto Packaging
plants. The Spillage that may occur during the
packing is collected into a spillage hopper
installed vertically
below, is than recycled to the system. The
packed bags are loaded into the trucks and or
transportation means
ultimately bound to the markets for sale.
|
|
|
Clinker Grinding Project at a Glance
(C.G.U.) |
|
Plants Offered (in MT/Day) |
100 |
200 |
300 |
600 |
900 |
1200 |
1500 |
2500 |
3000 |
Land
(Sq. M) |
4000 |
8000 |
10,000 |
16,000 |
20,000 |
24,000 |
30,000 |
50,000 |
60,000 |
Power
(kw) |
200 |
400 |
600 |
1200 |
1500 |
1,800 |
2,250 |
3,750 |
4,500 |
Gestation
Period |
6 - 8 |
9 -10 |
9 -10 |
9 -10 |
10-12 |
12-15 |
12-15 |
18-22 |
18-22 |
|
|
|
|
|
|
|
|
Raw Material (TPD) |
|
|
|
|
|
|
|
Clinker |
100.00 |
200.00 |
300.00 |
600.00 |
900.00 |
1200 |
1500 |
2500 |
3000 |
Gypsum
(approx 5%) |
5.00 |
10.00 |
15.00 |
30.00 |
45.00 |
60.00 |
75.00 |
125.00 |
150.00 |
|
|
|
|
|
|
|
|
Manpower
(for 3 shift) |
|
|
|
|
|
|
|
Administrative |
2 |
3 |
5 |
5 |
8 |
10 |
10 |
12 |
15 |
Technical |
3 |
6 |
9 |
9 |
12 |
15 |
15 |
18 |
20 |
Skilled
Worker |
4 |
6 |
9 |
12 |
15 |
18 |
20 |
22 |
25 |
Semi
- skilled |
18 |
21 |
24 |
24 |
28 |
32 |
35 |
38 |
40 |
|
Utilities |
Power
(kWh/T) |
30 - 35
|
Water
(lit/T) |
100
|
|
|
|